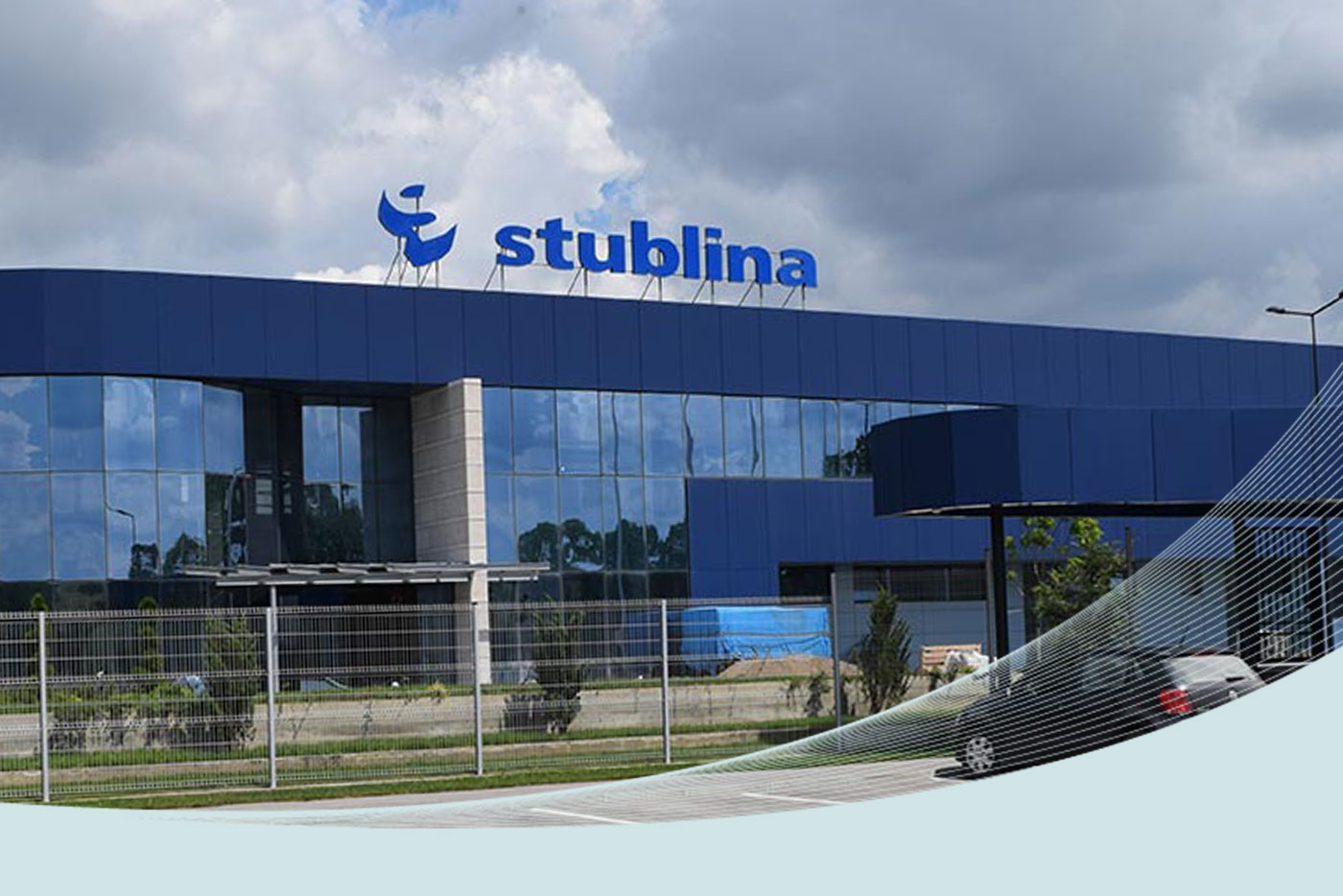
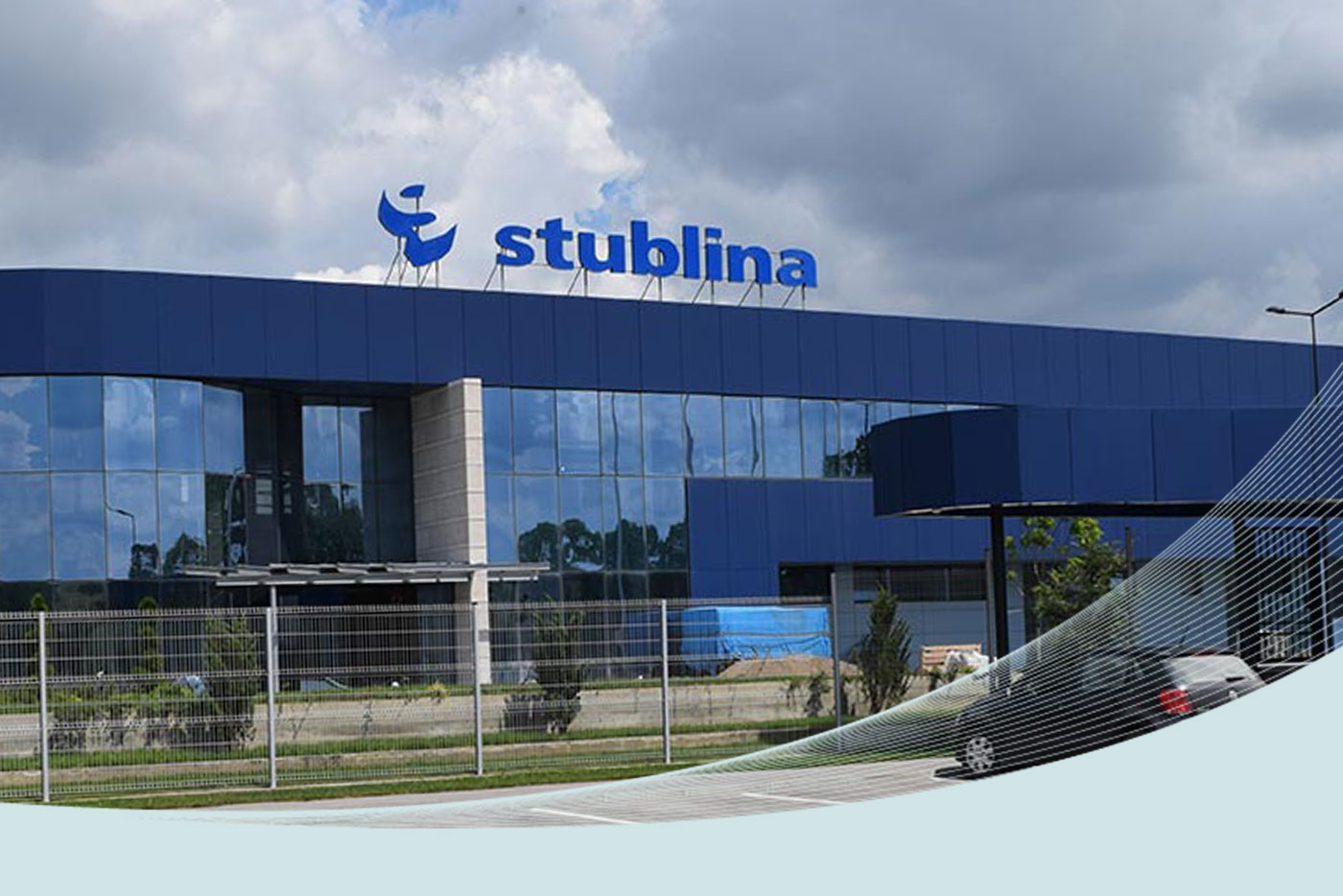
In the part intended for production, there is underfloor heating and cooling, ventilation of the foundry and other production and storage areas. In this part, the thermal energy recovery system from the production process was also designed and implemented. The primary source of energy is a water-to-water heat pump with a power of 240kW, and we got water from 4 wells over 120m deep with an accumulation of 40+40 cubic meters. A 160kW gas condensing boiler is installed in the power unit.
In addition, a complete internal gas installation for the needs of the boiler room, production lines for painting and metal melting machines was carried out. Underfloor heating, ventilation and air conditioning systems were installed in the office block.
In the part intended for production, there is underfloor heating and cooling, ventilation of the foundry and other production and storage areas. In this part, a system of thermal energy recovery from machines for casting brass and aluminum parts was also designed and executed.
For the needs of the production lines, we performed a complete installation of compressed air, internal and external hydrant network, as well as other installation for the needs of technology.